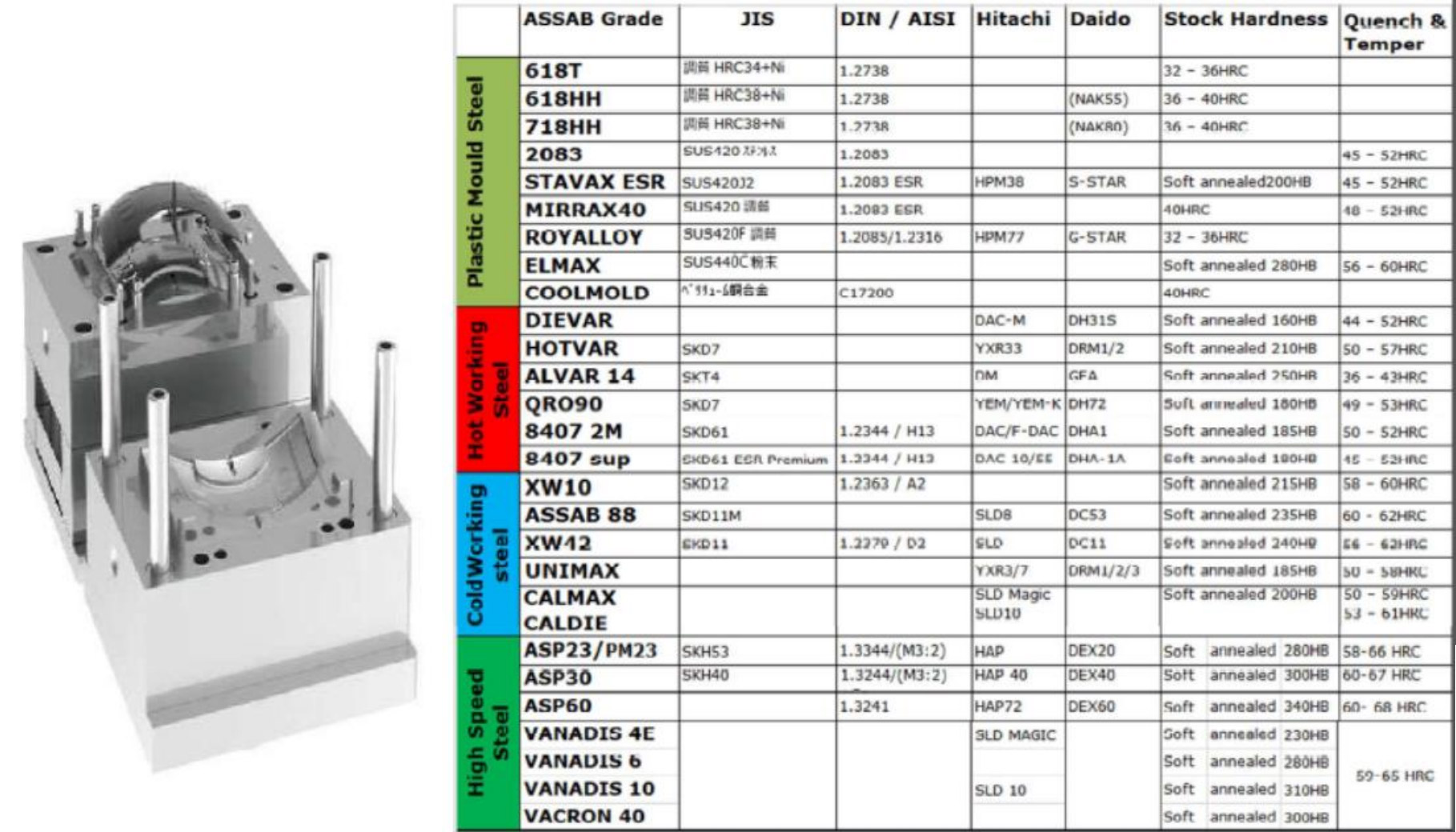
What is a jig?
A jig (lathe chuck) is a necessary technological equipment in the process of mechanical processing, inspection and assembly of mechanical products, used to determine the position of the workpiece relative to the cutting tool and hold the workpiece tightly. in a position under the influence of cutting force during machining.
Jigs contribute to improving the level of mechanization and automation of the precision mechanical manufacturing process. On machine tools, in order to cut, the detailed assembly process must be carried out. Therefore, jigs are an indispensable technological equipment in the processing process on metal cutting machines:
Used to quickly and accurately determine the position of workpieces on the machine
Used to guide cutting tools in drilling, boring, boring machines, etc.
Can create movements that do not exist on machine tools or do not work effectively
Ensure productivity requirements and reduce labor.
Improve the speed of mechanization and automation of production.
Expand the technological productivity of machine tools.
So the jig needs to meet two standards: good positioning and good clamping.
Small details - big impact
The jig is usually only very small in size in a machine but it has very important functions.
Fix the position of the positioned part, without external forces causing it to move or vibrate (clamp tightly), ensuring the exact position between the workpiece and the cutting tool.
Locate and guide cutting tools. Reduces extra time and machine time.
Create some extra motion to machine complex surfaces, taking advantage and expanding the machine's technological capabilities.
Reduce workers' labor intensity.
Reduces worker level requirements. Ensures precise positioning between workpiece and cutting tool. To complete such tasks (functions), jigs (fixtures) also need to have certain structural standards.
A jig will usually have the following general structure:
Positioning department.
Tight clamp set.
Power transmission mechanisms.
Guidance and comparison structures.
Rotating and grading mechanisms. Jig body and base.
Mechanism for positioning and clamping the fixture to the machine.
Classification of jigs:
Classification of jigs according to use: Depending on the use of jigs, they are divided into 3 types:
Classify jigs according to universal properties:
Universal jig: is a jig that can be used for many different types of parts. Universal jigs such as: vise, clamping jaw, rotating jig table, leveling head... Specialized jig: is a jig that is only used for one type of part.
Jigs are divided into 4 types according to the principle of clamping force transmission
Requirements for typical types of jigs
- Lathe jigs:
According to function the turning fixture can be:
The workpiece has rotational motion (chuck jig, jig connected to the main spindle of the lathe through the taper hole of the spindle).
Fixed workpiece, rotating knife (jig mounted on the slide of the lathe table).
Knife jig (image copying mechanism, quick knife retracting mechanism). The jig is mounted on the two centers of the lathe like a mandrel.
For jigs that are tightly attached to the main shaft of the lathe and have rotational motion, when designing, pay attention to measures to protect the machine and safety measures for workers.
Specifically, attention should be paid to centrifugal force, ensuring dynamic balance and that the details of the fixture do not have sharp edges.
The specific structure of the above jig is as follows: The jig connected to the main axis of the machine includes the workpiece positioning mechanism, the workpiece clamping mechanism, the jig body, the parts attached to the lathe, and the leveling mechanism.
The tool jig includes a universal knife table, a rotating head, a copy knife table, and a quick tool retraction mechanism when turning threads.
- Drilling jigs:
Drilling jigs are used on drilling machines to determine the relative position between the workpiece and the cutting tool, and to clamp the workpiece tightly for hole machining such as drilling, boring or boring. In addition to jigs, there are also other types of auxiliary tools to clamp knives such as clamps, quick clamps, and tapping clamps. Drilling jigs often limit all 6 degrees of freedom of the part to correctly determine the center hole of the machined part.
- Milling jigs:
When milling, the cutting force is large and the cutting is interrupted, causing large vibrations, so the milling jig must be sufficiently rigid. The structure of the milling jig includes: positioning mechanism, clamping mechanism, tool comparison mechanism, grading mechanism, copying mechanism, mechanism for placing the jig with the machine table (guide keys and clamping bolts). jig with T-slot of machine table)
- Grinding jig:
Grinding jigs usually come in 2 types Flat grinding: flat parts can be mounted directly on the magnetic table. For shaft details and complex details, use jigs placed on the magnetic table. Internal circular grinding: in this case, we use a speed clamp.
- Sharpening jig:
Due to the large broaching force, the work piece is tightly clamped thanks to the broaching force, the broaching jig does not need a clamping mechanism. Centering and guiding are both performed by the guide part of the broaching knife.
The structure of the broaching jig is simple, usually a silver, flange-shaped part to position the workpiece. When sharpening grooves, there needs to be a grading mechanism.